The Critical Role of Training and Accountability in Preventing Counterfeit Parts in Aviation
- Marco Taufer
- Nov 19, 2024
- 4 min read
Updated: Nov 29, 2024
In the wake of the aviation industry's response to the 2023 AOG Technics scandal, which exposed severe vulnerabilities in the global supply chain, the Aviation Supply Chain Integrity Coalition (ASCIC) was launched in February 2024. This initiative, led by aerospace industry leaders from the U.S. and Europe, aims to prevent unauthorized propulsion parts from entering the aviation supply chain and to strengthen the overall integrity of the supply chain.
The Coalition, composed of senior representatives from major manufacturers, including engine and airframe OEMs, maintenance, repair, and overhaul (MRO) shops, and regulatory bodies, issued a comprehensive report outlining 13 actionable recommendations. While the Coalition's work is commendable and essential, it raises a fundamental question: why is such an extensive effort necessary when the principles of traceability, documentation, and quality assurance are already detailed in existing standards like AS9120B?
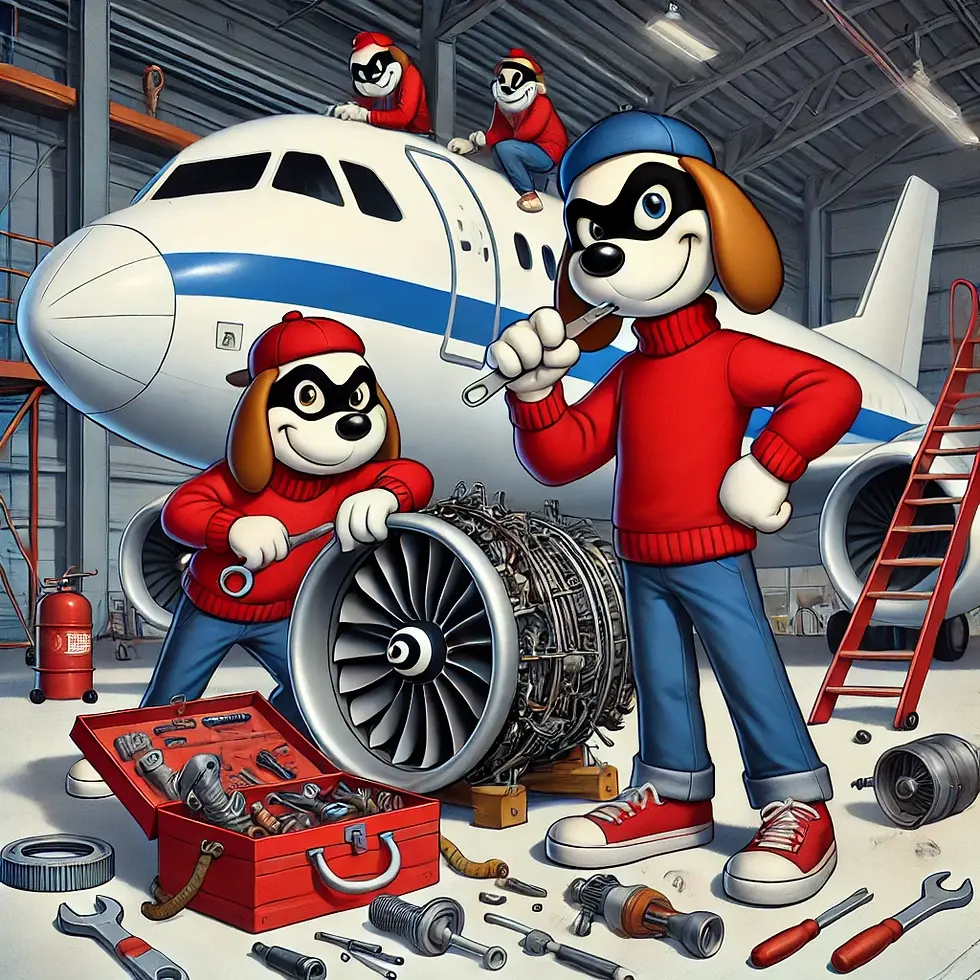
This is not the first time we’ve addressed the importance of supply chain integrity. In our previous blog article, 7 Things You Should Know Before Buying an Aircraft Part we discussed the AOG Technics scandal, its implications, and the critical considerations buyers must keep in mind to avoid counterfeit or unapproved parts. Now, with the Coalition’s work offering a new framework for action, it’s time to take the conversation further.
AS9120B: The Gold Standard for Supply Chain Safety
The guidelines outlined by the Coalition are not new. Every aspect mentioned—traceability, documentation, supplier accreditation, and risk management—is extensively covered in the AS9120B standard. This globally recognized standard specifies the quality management system requirements for stockist distributors and is designed to ensure that organizations handle aviation parts safely and reliably.
AS9120B in Practice
Any company that seriously implements AS9120B operates with a framework that inherently addresses the risks highlighted by the Coalition. The standard:
1. Emphasizes Traceability Ensures every part can be traced back to its source, reducing the risk of counterfeit or unauthorized components entering the supply chain.
2. Mandates Documentation Control Requires robust systems to manage and verify documentation, ensuring compliance with FAA, EASA, and other regulatory requirements.
3. Promotes Supplier Control Encourages rigorous evaluation and approval processes for suppliers, reducing risks associated with unverified vendors.
The issue, therefore, is not the lack of standards but rather the inconsistent implementation and understanding of these standards across the industry.
The Human Factor: Why Standards Alone Aren’t Enough
Despite the comprehensive framework provided by AS9120B, incidents like the AOG Technics scandal reveal gaps in its application. These gaps often stem from a lack of training and awareness among personnel responsible for implementing the standard.
Training Deficiencies
Through years of experience, many in the industry have encountered situations where even highly qualified personnel—Part 66 technicians, buyers, and accountable managers—exhibited doubts about fundamental aspects of traceability and documentation. While these cases may be rare, their existence points to a larger systemic issue: a lack of robust, ongoing training.
A striking parallel can be drawn to airline pilots. They do not rely solely on manuals for their training; instead, they undergo recurrent, rigorous training programs that include examinations to ensure competence. The same level of seriousness must be applied to supply chain personnel. Installing counterfeit parts is as dangerous as a pilot falsifying their credentials—both scenarios endanger lives and undermine trust in aviation.
The Culture of Compliance
Another challenge lies in the culture surrounding compliance. Many organizations view quality assurance and documentation as bureaucratic hurdles rather than critical safety measures. Without a culture that prioritizes safety and traceability, even the best standards can fail.
A Call for Licensed Procurement Professionals
The Coalition’s report undoubtedly provides valuable insights and actionable recommendations, but its impact depends on whether organizations and individuals implement them. This raises an important question: How can we ensure consistent compliance across the global aviation industry?
The Case for a Licensing System
One solution is to introduce a licensing system for procurement professionals, similar to the licensing requirements for pilots and technicians. Under this system:
- Buyers and procurement specialists would undergo mandatory training in supply chain integrity, documentation, and traceability.
- Licenses would be issued after passing a comprehensive examination.
- Ongoing education and periodic recertification would be required to maintain the license.
By establishing a formal credentialing system, the industry would ensure that only qualified individuals are authorized to make critical procurement decisions. This would also raise the overall professionalism and accountability within the supply chain.
Encouraging Adoption of Best Practices
While introducing a licensing system is a long-term goal, there are steps the industry can take now to address training gaps and promote the Coalition’s recommendations:
1. Mandatory Training Programs Companies should require all supply chain personnel to undergo training based on AS9120B and the Coalition’s report.
2. Digital Tools Expand the use of digital documentation systems to improve traceability and reduce errors.
3. Cultural Shift Foster a culture that views quality assurance as integral to safety rather than a mere compliance requirement.
A Unified Approach to Safety
The aviation industry has made significant strides in addressing the risks posed by unapproved parts, but more work remains. As we discussed in 7 Things You Should Know Before Buying an Aircraft Part, the AOG Technics scandal should serve as a wake-up call for the entire industry. The establishment of the ASCIC is a critical step forward, but its recommendations are only as effective as the individuals and organizations that implement them.
By fully embracing the principles of AS9120B and introducing a licensing system for procurement professionals, the industry can close the gaps that allow counterfeit parts to infiltrate the supply chain. The ultimate goal is to create a unified approach where safety is ingrained in every aspect of aviation—from the cockpit to the procurement desk.
Let us learn from the past and build a future where counterfeit parts have no place in aviation. Safety demands nothing less.
About Horix Aerospace
Horix Aerospace is an horizontally integrated aerospace company, strongly focused in Spare Parts Management solutions for the Business Aircraft Market. Horix has developed both the Trust Consignment Program and the Trust Dismantling Program to offer clients a unique opportunity becoming the Swiss Trusted Solution for Aerospace Components Management. With over USD 30M in assets under management, Horix Aerospace has become a disruptive force in the Aerospace Industry with both its Trust Dismantling Program and unique Business Model.
Strongly capitalized and managed by a team of industry veterans, Horix Aerospace is proud to be a Swiss owned and operated company.
Comments